Guided knife sharpening systems
Introduction
Sharpening systems with a guided abrasive are common among knife lovers and collectors, who sharpen their knives themselves. However, first of all, it is worth understanding what the concept of a "guide" as a technological unit is and what role this unit plays in the process of sharpening knives.
In industrial production, guides as a technological element are used a lot, both in large machine tools and in some handheld precision tools. One typical example is the dovetail connection.
Guides are used not only for the precise transport of machined parts in industrial machines, but also for the movement of units of various mechanisms up to their fine-tuning.
Guided sharpening systems pay a lot of attention to controlling the sharpening of the secondary bevels planes and the profiling of the cutting edge of the blade.
So, for example, in transport and supply systems speed and precision are required, while measuring and metal-cutting equipment requires precision and rigidity.
A guided sharpening system is a technological unit or device that helps you to sharpen cutting tools and control the process. The result can be repeated over and over again. Here is an example of this - the Veritas Mk. II device for sharpening of chisels on a water stone.

1. General purpose of guides for sharpening systems
Any guide increases the accuracy of a particular machining process and there are two types of guides of varying complexity and size found in sharpening machines:
- Horizontal guides
- Vertical guides
Horizontal guides allow you to control the sharpening process in a horizontal plane in relation to the blade. Technically speaking, the planes themselves may not be strictly horizontal during the sharpening process. This is only a relative term that defines the position of the blade in relation to the abrasive stone material. The sharpening process takes place at a certain angle to work with the plane of the secondary bevels. It is the guides with the abrasive stones that are positioned in the same plane with secondary bevels.
The vertical guides of the various brands of sharpening systems come in various designs and degrees of complexity. Any such design is intended to set the sharpening angle and control the movement of the horizontal guide.
The horizontal guide of advanced sharpeners is connected directly to the abrasive stones holder.
2. General description of the types of sharpening systems with guides according to size
Angle Guide Pocket Sharpener - Work Sharp Guided Field Sharpener, Benchmade, Work Sharp Pocket Knife Sharpener, Adjustable Angle Guide Hapstone T1

Pocket knife sharpeners can have 2 to 4 working surfaces. Often the first working surface is a tungsten carbide insert of about 400 grit. The second surface can have a grain size of about 1000 grit. The next option may be a ceramic surface for sharpening serrations. Some include diamond rods for honing of straight blades.

These sharpeners use special ledges at a certain angle on edges of the sharpener as guides. It is enough to press down on the blade and while maintaining the angle, slide it over the abrasive stone.

Similar, but not quite usual, would be the use of apex-type bars designed for professional systems. You can use these apex bars as well as a regular whet stone, or you can use a special clamp, like Hapstone T1 Adjustable Angle Guide. This device is similar to this type of sharpeners, but to work requires the abrasive stone to be put on a flat surface, it has a much more flexible use due to the possibility to use different abrasive stones. For sharpening it is enough to clamp the blade at a certain angle and you can start sharpening.
DMT Diafold type compact manual sharpening systems with guides and interchangeable abrasive stones kits - for knives from small to pocket ones with a blade of about 12 centimeters.

A separate group for knife sharpening tasks is the systems that combine some small size, sufficient functionality and ease of use. These systems use abrasive stones with an additionally attached guide in the form of a steel shaft.
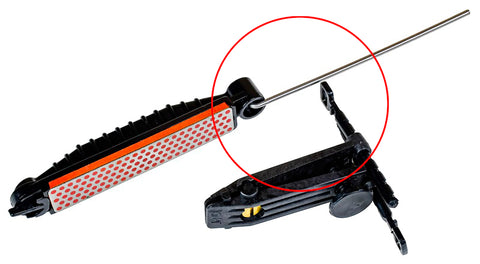
Some models have several fixed positions with specific angle values, and in the more advanced solutions, the sharpening angle can be adjusted.

The idea is that the blade is set in the clamp, and the abrasive stones holder and guide are set in the desired position. The sharpening can be done by holding in your hands or setting on a small flat surface for greater convenience.
Portable systems with vertical rods like Lansky Diamond / Masters;

Systems with so-called vertical rods have several significant advantages:
-
These systems have a base in which the rods are installed and do not need to be held.
-
There are several of these rods and they differ in grit size, abrasive stones material, profile shape and size, and honing angle.
-
The rods can be replaced if they are completely worn out.
-
The best way of keeping the consistent angle for honing.
Honing with such systems is much better than with a whet stone, and even better than the most advanced pocket sharpeners because of the length of the rods and their variability.

Some people may find the negative point to be much larger size and weight.
Work Sharp Benchstone Portable Angle Guided Sharpeners

The Work Sharp Bench stone has special ledges that are made at certain angles to the surface of the abrasive stone and serve as a kind of angle guides. It is enough to press down the knife and while holding the blade in this position run it several times on both sides of the surface of the abrasive stone to achieve a certain result. These guides make it much easier to work with the sharpener and do not require special training and a long getting used to as with a full-sized Bench stone.
Wicked Edge, KMFS RIVAL Portable Angle Guided Sharpeners with Two Abrasive Guides

When considering a sharpening tool like a guided system, one cannot ignore such ambiguous portable sharpening systems as Wicked Edge and KMFS RIVAL. Both systems practically copy each other and work with them seems to be quite simple and not much different from the DMT Fine Aligner with the difference that both systems are mounted on the base or attached to the edge of the table.

The ambiguity lies in the nature of the design itself and the principle of using abrasive stones in twos and not interchangeably. If it is not possible to purchase a single abrasive, you actually have to overpay and the entire system automatically becomes more expensive.
Besides, the whole design and sharpening technique highly question the comfort and precision of the work. Even if someone might find these systems interesting, it is difficult to recommend them directly, also because of the limited availability of non-universal abrasive materials.
Medium-sized sharpening systems based on Edge Pro magnetic table type

The cornerstone of many sharpening systems was the invention of Ben Dale, the Edge Pro sharpening system.
One of the main advantages of this sharpening system is the large range of abrasive stones that are manufactured on an industrial scale. As for the rest - it uses the principle of a horizontal guide with an abrasive holder and a vertical bar, on the basis of which the sharpening angle is adjusted.
With the introduction of this system, other brands began to develop more advanced modular systems.

Hapstone's Model M3 not only combines existing solutions, but has created the basis for a modular system. The M3 model represents one of the kit variants.
Both systems are equipped with a magnetic table with stops to fix the blade in the desired position for sharpening. Together with the horizontal and vertical guide, sharpening with these devices is quite close to professional sharpening systems, which also use Apex-type abrasive bars.
Household knife sharpening systems with Apex guides
- compact
- medium sizeย
- full size
One of the most technologically advanced groups of knife sharpeners is the mechanical or manual apex sharpening systems, which got their name from devices developed by a talented engineer a couple of decades ago and have become synonymous with the name of such sharpeners. These manual sharpening systems can basically be divided into three basic sizes:



All sizes of sharpeners have three identical units in their design:
-
guide with abrasive holder
-
vertical guide in the shape of an angle adjustment unit, in which the guide with the abrasive holder is mounted
- Semi-automatic turning mechanism with frame and clamps for fixing the blade of the knife

Some sharpeners in this group may be equipped with additional modules that allow additional adjustments:
- turning mechanism with a vertical position change in relation to the sharpening angle adjustment unit;ะด
- Some devices use a special toothed rack or a more complex rack lift to adjust the sharpening angle;
- Some rotary mechanisms have the option of horizontal offset in relation to the base of the sharpening device;
- Some models have a unit for adjusting the position of the base of the device over the work surface for use in combination with some natural abrasives;
- There are devices with a removable frame, which gives additional convenience of visual control of the knife;
- Some manufacturers have additional items and accessories for sharpening blades with complex geometry.
In addition, there are sharpeners that can be combined with items and accessories from different models of the same manufacturer to create a sharpener for your needs or for sharpening a knife of a certain size or shape of the blade.
The obvious advantages of using such systems are:
- High consistency of the sharpening angle due to the fixed position of the knife and the angle of the abrasive bar in relation to the blade, resulting in proper secondary bevels and a sharp cutting edge;
- The abrasive guide with abrasive holder makes work easy;
- Using special-type bars makes it possible to shape the secondary bevels easily, to perform precise finishing of the secondary bevels, as well as re-profiling if the cutting edge is damaged;
- The stepless adjustment of the sharpening angle and the adjustable blade clamping allows you to sharpen blades of different types and sizes.
Compact systems are used wherever small size, light weight and the ability to sharpen small and medium-sized knives are most important. The main advantage is the size of the clamps and the size of the clamping frame. Sharpening a knife, especially a small one with a thin blade, will be much easier to implement on such a device than on others. Such sharpeners will definitely find their place in the home kitchen.
Medium-sized sharpening systems, as compared to full-size sharpeners, are most often distinguished by a holder for an abrasive stone of a certain standard, angle range. Some also have a turning mechanism. Sharpeners can be used in workshops for sharpening small series of various knives with some limitations.
The difference between medium-sized and full-sized sharpeners is somewhat more difficult to distinguish, and price is not the main reason. First you have to decide what sharpener you need and then you have to decide how much you want to spend.
Large, full-size devices are obviously the most optimal, since they can cover the widest possible range of knives of different lengths and geometries.
The main features to distinguish between all sizes of sharpeners are:
- Weight - the bigger the system, the heavier it is, but also more stable;
- Sharpening angles range - the larger the overall dimensions of the device, the greater the range of sharpening angles
- The difference in the size of the frame and clamps - the possibility to sharpen knives with great convenience with different width, thickness and length of the blade;
- Compatibility of clamps of certain models of the same manufacturer - the possibility of combining and adjusting the system to the specific task;
- Different dimensions of the units in the assembled condition affect, in one way or another, the choice of workplace and arrangement of the sharpening accessories and other items.
Sharpening systems equipped with guides, especially professional apex-type devices, are complex devices with a number of similarities and differences. The very number of technical features, and particularly the possible combination of them, requires a certain level of understanding of their purpose.
Those who intend to use such sharpeners should understand that, with experience and the right abrasives, the output quality of such systems is much higher than all others.
3. A short list of the leading brands for professional guided sharpening systems
There are a small number of manufacturers in the world of genuine quality guided sharpening systems. These include TS Profil (TSPROF), Kazak Poland, Hapstone, Gridviva, ZigZag Max, Magna-Tec and several others.
Summary
Choosing a professional device for sharpening knives is a very serious matter indeed. It is necessary to understand that using this or that equipment you can achieve similar results of sharpness of knives with different speed. In this case, your personal skill and understanding of sharpening technology will be decisive, because the work is done not by the device, but by a man. You just need to understand the essence and principles of knife sharpening, to understand what result you want to achieve at each stage. The truth is that if you do not know how to sharpen knives, then it will be equally difficult to work with simple devices and expensive professional ones. No machine will give you skills, otherwise you would not need to learn, because human skill and quality abrasives are in the first place, and the equipment itself is in the second place.
Besides, it is also necessary to understand that any item has its own dimensions and requires an appropriate workplace. In addition to the device itself, there will be a need for storage space for items like accessories and consumables for several reasons: for safety, work hygiene, and personal convenience.
Professional knife sharpening systems and knife sharpeners, combined with high-quality consumables and accessories, will work best in capable hands, and it can be learned if desired. In the end, it can be an interesting hobby, and someone will make a business out of it, combining the useful with the pleasant. A properly sharpened knife is the result of labor, knowledge, and skill.