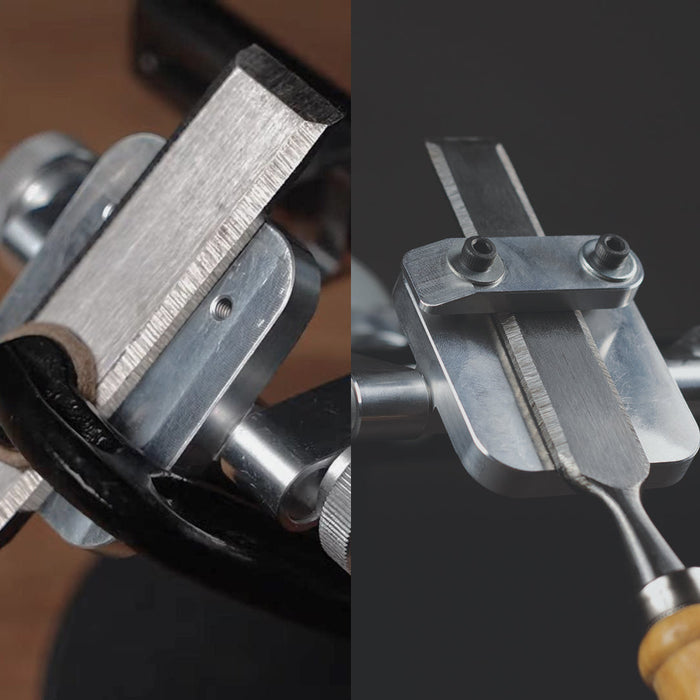
Tool Sharpening
Sharpening of Cutting Tools The use of any cutting tool inevitably leads to wear and a reduction in the sharpness of the cutting edge. The cutting edge is the working part of the tool, formed by the convergence of two...
Today you can find a number of different professional sharpening systems and devices that are used for sharpening of a wide range of cutting tools.
However, before we start reviewing them, it is worth getting to the bottom of what any professional device actually is.
First of all, the concept of a "professional device" can be compared with the concept of a "high-precision device". A professional sharpening device must have a high level of manufacturing quality and a precise fitting of parts to perform knife sharpening with proper quality.
Only if such qualities are present we can say that this device is intended for professional use or it can be used for running your own sharpening business or for personal purposes.
Among all existing devices there are two main groups, which are capable of sharpening the blades of various cutting tools different in their design principle:
Regardless of the design, all professional sharpening systems and devices are divided into:
Within this group we can also divide them into separate categories, since some are more versatile and some can only be used for narrowly-specialized knife sharpening. In addition, some devices have some units similar in their application to other devices, however they work in a different way.
For a better understanding of this type of sharpeners, it is worth listing their main features:
To conclude, we can note that sharpeners of this type are quite often used in home kitchens, while the more expensive and advanced ones are used in restaurant kitchens. Quite often restaurants have one or more sharpeners, which is due to the nature of the work and as a technical solution is quite acceptable in terms of cost.
In the home kitchen, the use of more expensive sharpeners is impractical.
This solution can generally be recommended when using in the kitchen not expensive chef's knives and if there are no special requirements for the condition of the secondary bevels and the cutting edge.
It has been repeatedly verified that the life of even the most advanced sharpeners in regard to the primary biting condition of the edge drops after sharpening 100—200 knives (less advanced sharpeners with aluminum oxide abrasive discs have a much shorter life). In other words, once the abrasive plates enter the working tempo, you will not be able to get the cutting edges of the knives as sharp as before and the maximum service life is about 3000 knives.
Technological evolution has undoubtedly provided a number of design improvements and increased the efficiency of electric desktop sharpeners, but all electric sharpeners of this kind have retained the technical problem of their predecessor in one way or another.
The main features of this type of sharpening systems are functionality, versatile use and high accuracy, which are ensured by a number of the following properties:
Variety and versatility
The sharpener with use of different parts can be set up for sharpening a number of different cutting tools and knife blades of different types and sizes. A range of sharpening discs on different bonding agents also makes it possible to work with steels of different hardness. Some manufacturers have separate models designed specifically for sharpening kitchen and chef knives for use in large restaurant and hotel kitchens.
Consistency and accuracy of sharpening angle adjustment
High level of consistency and accuracy of angle adjustment is a feature of quality machines of this kind. The higher quality and more expensive sharpeners have the motor and shaft located under the metal part of the body on which the universal support is mounted. This technical solution provides stable fixation of the universal support with the possibility of adjusting the height above the device. This supporting guide rod is the basis for all types of sharpening work. Knife blades get clamped in suitable fixtures which are guided along the rod. This technique ensures a smooth stroke and a consistent sharpening angle.
Low RPM and quality control
Low revolutions of 100 - 200 rpm enable gradual gentle machining during the sharpening process, which gives the precise control over the result of the work. The low speed of the sharpening wheel also minimizes the possibility of overheating the cutting edge and the knife blade as a whole, because the spot of contact with the sharpening wheel is quite large.
RPM support and adjustment
Leading manufacturers' sharpeners are equipped with special electronic RPM support to ensure consistent sharpening quality even under high loads. Some sharpeners are equipped with speed adjustment.
Water cooling
The cooling of this type of systems is provided by special grinding wheels designed for sharpening with water mainly for stainless steels. Cooling is also necessary because of the high torque and the mentioned large contact area. Both factors ensure a high efficiency of the sharpener and a high level of knife sharpening quality and thus require water cooling. In addition, the water removes metal and stone particles from the abrasive wheel and prevents it from getting clogged.
Safety and low noise level
All residual abrasive material collects in the water pan and no dust is released into the air. Besides, no sparks are generated, which can be dangerous in certain conditions. Beyond that, the high quality machines are almost silent.
Relative portability
The sharpening machine is quite transportable due to its relatively low weight and can be used outside the workshop. At the same time such a machine and its accessories require a certain workplace, which should be taken into account before purchase.
Learning how to use such a sharpener will certainly take some time, but the investment will definitely pay off if you want to do small projects or small batches. The use of the sharpener in stream production is definitely not recommended, even in spite of the manufacturer's significant warranty period.
Flaws of water-cooled sharpeners
The flaws include the fact that the cost of quality sharpeners and their parts is quite high. Some manufacturers, due to the demand, produce their devices at a cheaper price and sometimes with a significant loss in quality and design flaws.
Also, cheaper brands do not offer the full range of possible parts and accessories. It is possible to use parts from other brands, but this is not always advisable. The comparison of using, for example, very expensive car tires on a medium-lower quality vehicle is somewhat relevant here.
In order to properly sharpen a knife with different grit sizes, it is necessary to change the abrasive wheel to a wheel with a smaller grit size, which takes a certain amount of time and readjustment of the machine. The way out can be the purchase of one or more sharpeners or use in conjunction with other units. For example, it can be a quality sharpener with a polishing wheel of different surfaces for deburring and polishing the blade.
Such finishing is often used for commercial application of devices.
To sum up the points above, before selecting and purchasing this kind of sharpener, you should first check:
You can also avoid possible technical defects by purchasing an initially high-quality device with the ability to buy the necessary accessories and supplies.
This group of sharpeners has some similar technical features to the sharpeners described above.
These machines mostly use Japanese water abrasive disc with characteristic properties. The main feature of these machines is that the device operates at low speeds.
One of the disadvantages, in contrast to the vertical arrangement of the abrasive wheels, is that there is no stable support guide and only the side plane of the wheel is used. In this mode, comfortable and relatively accurate sharpening is possible only for knives and cutting tools. Working with small blades remains a very difficult task, because small blades need to be held by hand, which requires certain skills.
Some manufacturers do have various holders, guides, and other accessories for precise work.
If you compare the principle of work with electric desktop sharpeners using the side plane of the sharpening wheel, the difference lies in the diameter and material of the abrasive wheel, which is a noticeable advantage. In addition, sharpening marks will always form on any blade at a certain angle depending on the location to the sharpening wheel. You can achieve a fairly good level of knife sharpening with good and biting sharpness using abrasives available for such machines. Such sharpeners may well occupy their niche for certain purposes, e.g. in carpentries, leatherworking shops or in places where the condition of the secondary bevels and the cutting edge is not of high concern.
It is also worth mentioning that sometimes you can find interesting technical solutions that combine a classic desktop sharpener with the unit, in which the grinding disc is located in a horizontal position with the possibility of water supply. Some have the possibility of adjusting the support not only at a certain angle, but also at a height above the tool.
It is advisable to have a workplace for all such sharpeners, because it is impossible to exclude water splashing and the desktop must be as vibration-resistant as possible in the horizontal plane.
Such equipment is designed primarily for sharpening the blades of hair clippers, meat grinders, wire cutters, surgical tools, coffee grinders, etc.
The features of such sharpeners are:
There are some hybrid versions among these types of machines that are more similar to table sharpeners with two vertical discs on a shaft. The technology itself allows the use of a disc, also in a vertical position. These machines are designed to perform a fairly wide range of work, depending on their use with different holders.
Belt-sanding machines and grinders among all electrically driven devices stand out for their maximum efficiency. A wide range of different materials for the manufacture of grinding belts, extends the application area, from aggressive metal removal and reprofiling to grinding and polishing.
Apex-format mechanical or manual knife sharpening systems can be classified as one of the most technologically advanced groups of knife sharpeners, which got their name from devices developed by a talented engineer a couple of decades ago and have become synonymous with the name of such sharpeners. These manual sharpening systems can basically be divided into three basic sizes:
The design of such devices consists of a base, on which the vertical mechanism for adjusting the angle of the abrasive guide with the abrasive holder and the rotary mechanism is mounted.
More than 30 years have passed since this type of sharpeners appeared, and since technical progress never stops, new ideas and developments appear. There are a number of manufacturers on the sharpening system market with devices of various applications.
Some knife sharpeners are equipped with additional units that allow you to make additional adjustments:
There are systems of sharpeners, which can be upgraded and combined with parts of different models of the same manufacturer and create a sharpener to suit your needs or for sharpening a knife of a certain size or shape.
The obvious advantages of using such systems are:
Compact systems are perfect for those who need a device of small size and light weight to sharpen small and average knives. The main advantage is the size of the clamps and the clamping frame. Sharpening a knife, especially a small one with a thin blade, will be much easier to carry out with such a device than with others. Such sharpeners will definitely find their place in the household.
Medium-sized sharpening systems, in comparison with full-size sharpeners, are most often distinguished by angle range and by an abrasive holder of a certain standard. Some also have a turning mechanism. Sharpeners can be used in workshops for sharpening small series of various knives with some limitations.
The difference between medium-sized and full-sized sharpeners is somewhat more difficult to distinguish, and pricаe is not the main factor. First you have to decide what your goals are, and then you need to determine your budget.
If you consider the question of the differences of this class of sharpeners as a whole, the large, full-sized devices are obviously the most convenient, because they can cover the widest possible range of knives of different lengths and geometries.
The main points of difference between the sharpeners of all sizes are:
Professional sharpening systems of the apex format are complex devices with a number of similarities and differences. The very number of technical parameters and even more so their possible combinations require a certain level of understanding of their purpose.
For those who intend to use such sharpeners, should understand that with experience and the right abrasives, the output quality of such systems is much higher than all others. This also means that a certain quality will always cost a certain amount of time for manual work, so the price of the service for properly sharpened knives will be corresponding.
Choosing a professional device for sharpening knives is a very correct and serious question. It is necessary to understand that using this or that equipment it is possible to achieve similar results of knife sharpness at different speeds. In this case, your personal skill and understanding of sharpening technology will be crucial, because in the end the work is performed by a person, not a device. You just need to understand the essence and principles of knife sharpening, to understand what result you want to achieve at each stage. The truth is that if you do not know how to sharpen knives, then it will be equally difficult to work with any device regardless whether it is cheap or expensive. No machine will give you the skills, otherwise you would not need to learn, so human skill and quality abrasives matter the most, and the equipment itself takes second place.
Besides, it is necessary to understand that any equipment has its own dimensions and requires an appropriate work space. In addition to the device itself, you will need a storage place for accessories and supplies for several reasons: for safety, work hygiene, and personal convenience.
Professional knife sharpening systems and knife sharpeners, combined with high-quality supplies and accessories, will be a powerful tool in capable hands. It can become an interesting hobby, and for someone a business that combines the useful with the pleasant. A properly sharpened knife is the result of labor, knowledge and skill.
Sharpening of Cutting Tools The use of any cutting tool inevitably leads to wear and a reduction in the sharpness of the cutting edge. The cutting edge is the working part of the tool, formed by the convergence of two...
Slip stones are special sharpening stones designed for sharpening special cutting tools, such as woodworking equipment. They come in various shapes and sizes. Learn more about their types and purposes in this article.
A file or a special abrasive? In the world of sharpening, the word "file" might sound a bit out of place, especially for those not too familiar with hand tools. Most people would associate it with a rough metalworking tool,...
{"one"=>"Select 2 or 3 items to compare", "other"=>"{{ count }} of 3 items selected"}